Quality Policy
Customer oriented for achieving customer satisfaction -
Improving manufacturing technology for superiority in product quality Implementing full participation for business culture of excellent quality
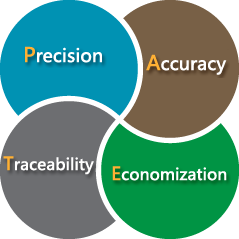
Quality Management
- Quality inspection management standard
- Correction and prevention management standard
- Contracted processing management standard
- Shipping management standard
- Disqualification product qualification management standard
Quality Objectives
- Product yield rate reached more than 95%
- Customer satisfaction rate reached more than 95%
- Delivery rate reached more than 95%
Quality Inspection Project
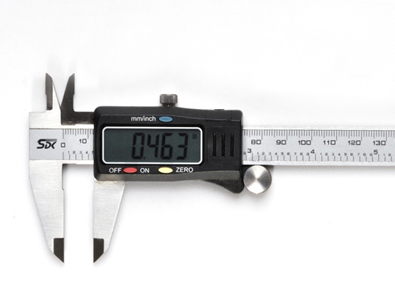
1. IQC
Supplier product quality management (source material)-
Perform inspection according to the inspection rules for material specification of the official drawings, appearance, sample for approval, limit sample (according to the sampling standard of MIL-STD-105E AQL:1.0).
Incoming quality management (contracted processing product)-
Perform inspection according to the official drawings and inspection rules, sample for approval, limit sample (according to the sampling standard of MIL-STD-105E AQL:1.0).
2. OPQC
Perform sampling inspection at a rate of 10pcs per 2 hours according to the official drawings and inspection rules, sample for approval, limit sample, and recording in the “OPQC manufacturing process inspection record table”, followed by executing according to the “manufacturing management procedure”.
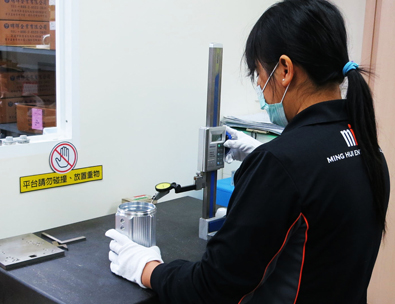
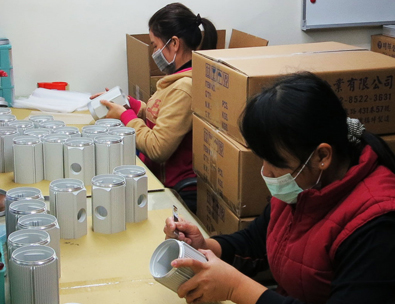
3. QC
Performing quality inspection and packaging process according to the packaging process standard and inspection rules; indicating the date, product name and quantity on the product labeling form; out-going inspection performed by QA.
4. QA
Performing inspection according to the appearance inspection rules of the operation standard (according to the sampling standard of MIL-STD-105SE AQC:1.0).
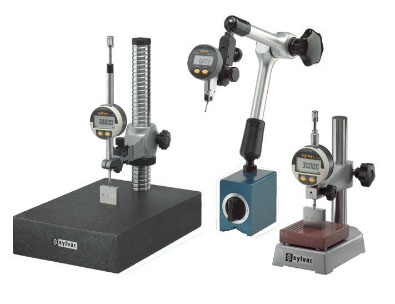